UX designer / Product designer
Printing at the warehouse
User experience for printing documents and labels at a warehouse

Background
This was the case I worked on during my 8-week-long internship at Consafe Logistics as part of the UX Design program.
Consafe Logistics is a software company that provides solutions for warehouse management operations, administration, and control. Warehouse operators, the target group of users, use the product called Astro WMS®, which is extremely powerful, however, complex, and requires a great deal of technical understanding. New users make mistakes rather easily, lose time figuring out the system, and often need assistance to be able to work. The UX team has been tasked to design a modern user interface for warehouse operations that builds on the Consafe Logisitcs’ strong technical platform and sharp product functionality to improve the current user experience.
Problem
At the warehouse, various labels and documents are printed and used in a variety of processes. Users today do not get any feedback when labels are printed on the clients. There is no simple way of knowing which printer the device is connected to. The current way of pairing a device with a label printer is an advanced process that has to be done by a superuser.
Goal
The goal of this project was to tackle the challenge of using Design Thinking methodology and utilizing internal resources such as subject matter experts and qualitative data from the previous research done by other designers at Consafe Logistics. My personal goal with the project was to focus on concept development and improve my prototyping and visual data presentation skills.

How might we
Improve the user experience of printing for the warehouse operators?
My process
During the internship, I attended several workshops with both the UX team and the wider project team and took part in the discussions. This gave me the opportunity to get to know the team and orientate myself in the new-to-me field of logistics and its terminology. I followed the Design Thinking process.
To gather my first impressions of the product, I performed a pilot study of the subject from the material sent to me in advance and prepared initial questions for future interviews. Upon studying the terminology, I analyzed the variety of physical printers, labels, and documents printed in different processes and today’s flow of re-connecting and configuring the printer.

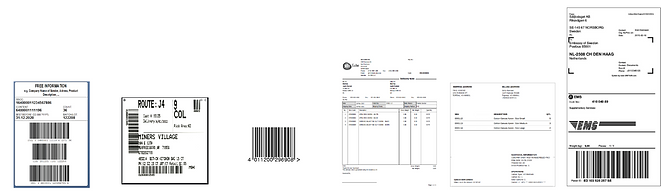

As a next step, I performed a series of interviews with subject matter experts and former warehouse operators. Missing the qualitative data directly from the target group, due to a not-yet-established recruitment channel, I decided to make sense of problems using a Problem-error assumption exercise. So, I made a list of assumptions, listing what errors might happen when a new user comes across a printing problem in their work as a way to understand the various problems’ consequences and severity. Synthesizing all the data from interviews, I created a user persona, Johnatan, a new seasonal warehouse employee.

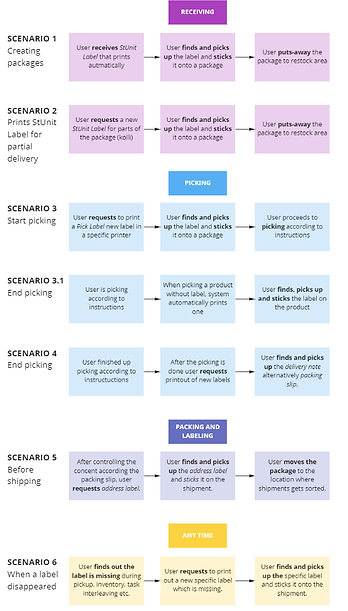


I formulated a couple of How might we questions to spark the ideation and ended up sketching three different solutions: one conservative, one wacky, and one middle ground. Settling on creating a wizard flow solving configuration issue I started with creating a flowchart and prototype in Balsamiq.

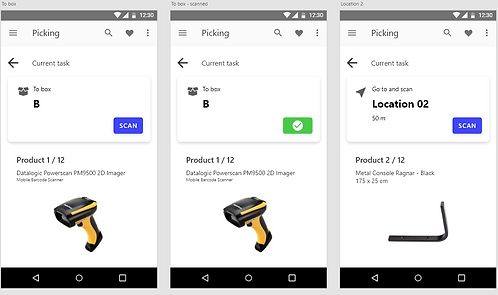
I recruited two test participants with limited or no experience with working in a warehouse. Utilizing a small in-house warehouse, I prepared the necessary physical props and tested the prototype. In the prototyped scenario, the printer was not able to print the requested label, a user would be helped with a troubleshooting flow that takes them through three extra steps as opposed to finding a superuser to help them and solve the configuration problem for them. The idea was to see how the testers would react and how they could, with the help of UI solve the problem. Taking into consideration the feedback from my testers, I translated the lo-fi prototype into hi-fi in XD and made multiple adjustments. Due to the lack of time, no more usability tests were performed.

Result
The work resulted in a better understanding of the printing process and related flows in a warehouse. If implemented, the benefits of this solution could result in lower expenses on hardware maintenance for Consafe Logistics and staff would have time to focus on more serious troubleshooting or testing activities. As for customers, the solution would save the superuser’s or system administrator’s time as they would not need to troubleshoot the system from scratch in a 16-step process each time. As for the target user, no knowledge or training to configure a printer would be needed, the solution saves workers’ time spent on physical reporting. Solving a connection problem with the proposed solution might seem trivial – not being able to solve it is being experienced as a stressful situation for the worker. The solution would decrease or eliminate user’s frustration and help him stay in the flow with minimal interruption.
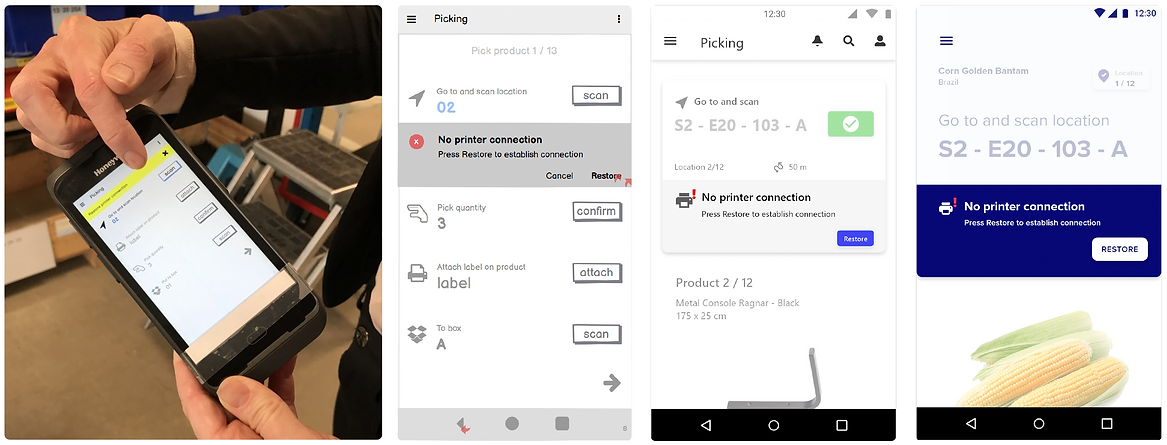
Methods
design thinking, heuristic evaluation, context mapping, prototyping, usability testing
Tools
MIRO, Balsamiq, Adobe XD, Illustrator
Duration
8 weeks, 2021